Gypsum
The sequence of operations in three-coat gypsum
plastering is as follows:
1.
2.
3.
4.
5.
6.
7.
8.
9.
10.
11.
Lime
Install the plaster base.
Attach the grounds.
Apply the scratch coat approximately 3/16 inch
thick.
Before the scratch coat sets, rake and cross
rake.
Allow the scratch coat to set firm and hard.
Apply plaster screeds (if required).
Apply the brown coat to a depth of the screeds.
Using the screeds as guides, straighten the
surface with a rod.
Fill in any hollows and rod again.
Level and compact the surface with a darby;
then rake and cross rake to receive the finish
coat.
Define angles sharply with an angle float and a
featheredge. Trim back the plaster around the
grounds so the finish coat can be applied flush
with the grounds.
The steps for lime base coat work are similar to
those for gypsum work except that, for lime, an
additional floating is required the day after the brown
coat is applied. This extra floating is required to increase
the density of the slab and to fill in any cracks that may
have developed because of shrinkage of the plaster. A
wood float with one or two nails protruding 1/8 inch
from the sole (called a devils float) is used for this
purpose.
Portland Cement
Portland cement plaster is actually cement mortar.
It is usually applied in three coats, the steps being the
same as those described for gypsum plaster. Minimum
recommended thicknesses are usually 3/8 inch for the
scratch coat and brown coat, and 1/8 inch for the finish
coat.
Portland cement plaster should be moist-cured,
similar to concrete. The best procedure is fog-spray
curing. The scratch coat and the brown coat should both
be fog-sprayed cured for 48 hours. The finish coat
should not be applied for at least 7 days after the brown
coat. It too should be spray-cured for 48 hours.
FINISH COAT APPLICATION
Interior plaster can be finished by troweling,
floating, or spraying. Troweling makes a smooth finish;
floating or spraying makes a finish of a desired surface
texture.
Smooth Finish
Finish plaster made of gypsum gauging plaster and
lime putty (called white coat or putty coat) is the most
widely used material for smooth finish coats. A putty
coat is usually applied by a team of two or more persons.
The steps are as follows:
1.
2.
3.
4.
5.
6.
7.
8.
One person applies plaster at the angles.
Another person follows immediately, straight-
ening the angles with a rod or featheredge.
The remaining surface is covered with a skim
coat of plaster. Pressure on the trowel must be
sufficient to force the material into the rough
surface of the base coat to ensure a good bond.
The surface is immediately doubled back to
bring the finish coat to final thickness.
All angles are floated, with additional plaster
added if required to fill hollows.
The remaining surface is floated, and all hollows
filled. This operation is called drawing up. The
hollows being filled are called cat faces.
The surface is allowed to draw for a few minutes.
As the plaster begins to set, the surface-water
glaze disappears and the surface becomes dull.
At this point, troweling should begin. The
plasterer holds the water brush in one hand and
the trowel in the other, so troweling can be done
immediately after water is brushed on.
Water is brushed on lightly, and the entire
surface is rapidly troweled with enough pressure
to compact the finish coat fully. The troweling
operation is repeated until the plaster has set.
The sequence of steps for trowel finishes for other
types of finish plasters is about the same. Gypsum-finish
plaster requires less troweling than white-coat plaster.
Regular Keenes cement requires longer troweling, but
quick-setting Keenes cement requires less. Preliminary
finishing of portland cement-sand is done with a wood
7-15
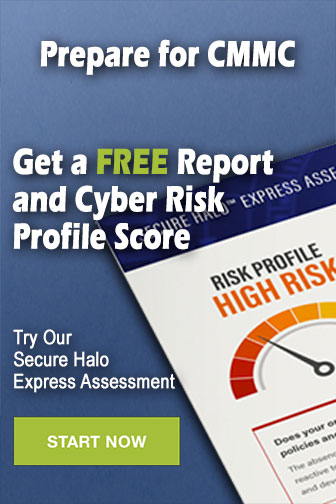